Can End
Aluminum and Tinplate can ends
7/11/2024
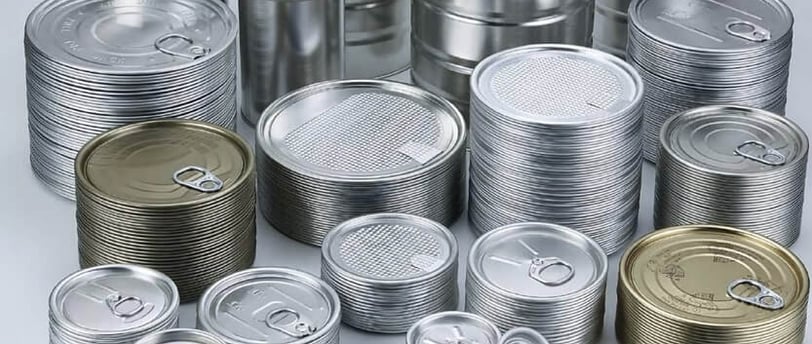
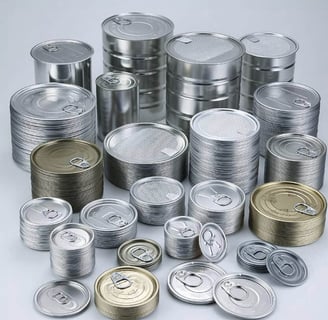
Can End
The end of an aluminum or tinplate can, often referred to as the "can end," plays a crucial role in the packaging of food and beverages. These ends are an integral part of the can’s overall design and functionality, providing both preservation and convenience. The development and design of can ends have evolved significantly over the years to enhance product safety, extend shelf life, and meet consumer demands for convenience and sustainability.
Design and Functionality
The can end is designed to create a hermetic seal that protects the contents from external contamination and oxidation. This seal is essential for maintaining the freshness, flavor, and nutritional value of the food or beverage inside. The can end typically features a double-seam construction, which involves folding and sealing the can end to the body of the can. This method ensures that the contents are securely enclosed, preventing leaks and preserving the integrity of the product.
In aluminum cans, the end is often made from a thin, lightweight sheet of aluminum, which is both strong and malleable. Aluminum is favored for its excellent barrier properties, resistance to corrosion, and recyclability. Tinplate cans, on the other hand, are made from a steel base coated with a thin layer of tin. This coating helps prevent rust and corrosion, although aluminum is more commonly used in modern can production due to its superior performance and lower cost.
Technological Advances
Technological advancements have significantly improved the design and functionality of can ends. For instance, the introduction of easy-open ends, also known as pull-tab lids, revolutionized convenience in the food and beverage industry. Before this innovation, consumers had to use can openers to access the contents, which was often cumbersome and less practical. The pull-tab mechanism allows consumers to open cans easily with minimal effort, enhancing user experience and accessibility.
Moreover, the development of beverage cans with resealable ends has catered to consumer preferences for portion control and convenience. Resealable cans allow users to enjoy a portion of the beverage and securely close the can to preserve the remaining contents. This feature is particularly popular in beverage cans for products like soda and energy drinks.
Sustainability Considerations
Sustainability is a key concern in the production and disposal of can ends. Aluminum and tinplate cans are highly recyclable, and the recycling process for these materials is well-established. Recycling aluminum is particularly energy-efficient, as it requires only a fraction of the energy needed to produce new aluminum from raw materials. Tinplate cans are also recyclable, but the process can be more complex due to the need to separate the tin coating from the steel base.
Efforts are being made to improve the environmental footprint of can ends by reducing the amount of material used and increasing the efficiency of the recycling process. Innovations such as lightweight can ends and the use of recycled materials in production are steps towards minimizing environmental impact. Additionally, advancements in coating technologies have led to the development of more eco-friendly and less harmful coatings for can ends.
Consumer Impact and Market Trends
The design and functionality of can ends directly impact consumer experience. The ease of opening, the effectiveness of the seal, and the convenience of resealability all contribute to user satisfaction. As consumer preferences evolve, manufacturers continually adapt their designs to meet market demands, incorporating features that enhance usability and product protection.
In conclusion, the can end—whether made of aluminum or tinplate—plays a vital role in food and beverage packaging. Its design ensures product safety, convenience, and preservation. Technological advancements and sustainability efforts have further refined the functionality of can ends, addressing consumer needs and environmental concerns. As the industry continues to innovate, can ends will likely see continued improvements in both performance and environmental impact, reflecting broader trends in packaging technology and consumer preferences.
Easy Open Ends
Manufacturer and exporter of easy open ends.
Contact
Email us today
EMAIL:director@packfine.com
TEL +86 13054501345
WhatsApp +44 7845 239331
© 2024. All rights reserved.
If need aluminum cans, please go to www.packfine.com